Bringing Manufacturing Back to the United States
Since the 1970’s, the globalization and offshoring of domestic manufacturing & production processes has been a popular means for businesses to attempt to lower labor costs and maximize profits but in a post-pandemic world, this decades-long dependence on overseas manufacturing is no longer viable.
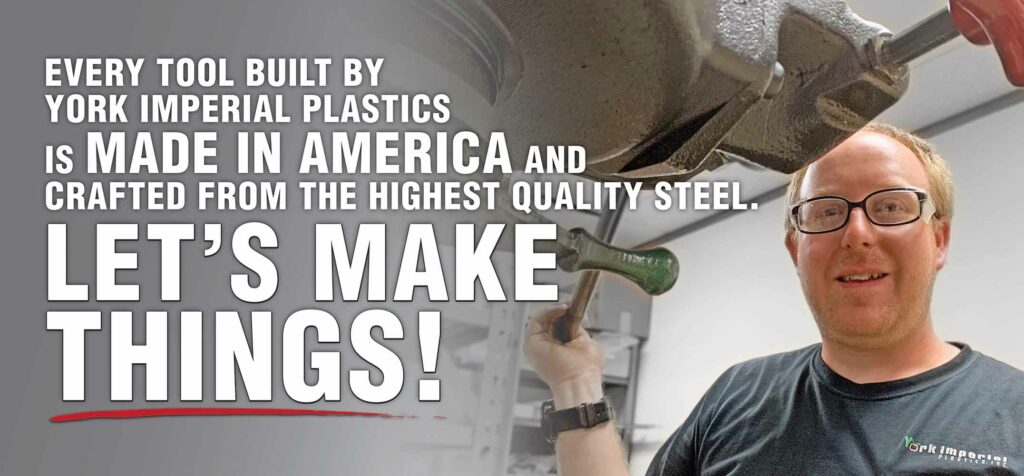
According to Shale Crescent USA, a 2022 study names the United States as the most profitable place to manufacture plastics products. This news has narrowed the gap between the offshore market and the domestic United States prompting companies to bring tooling, manufacturing & production processes back from overseas, also known as reshoring, thanks to the supply-chain issues that have resulted from the COVID-19 global pandemic.
The Tipping Point
Although there are many injection molding facilities located offshore who will entice companies with offers of lower-cost labor and production, when choosing an injection molder, there are a few factors that should be considered long term, such as the in-bound/out-bound shipping and delivery fees of materials and parts, lead times on the production process, the level of customer service, and most importantly – quality standards.
There are more factors to consider than simply dollars and cents such as risk management, strategic direction, and overhead just to name a few. Offshore manufacturing, production and tooling options ultimately result in more headaches & higher costs overall for everyone involved due to quality & consistency issues in the production process.
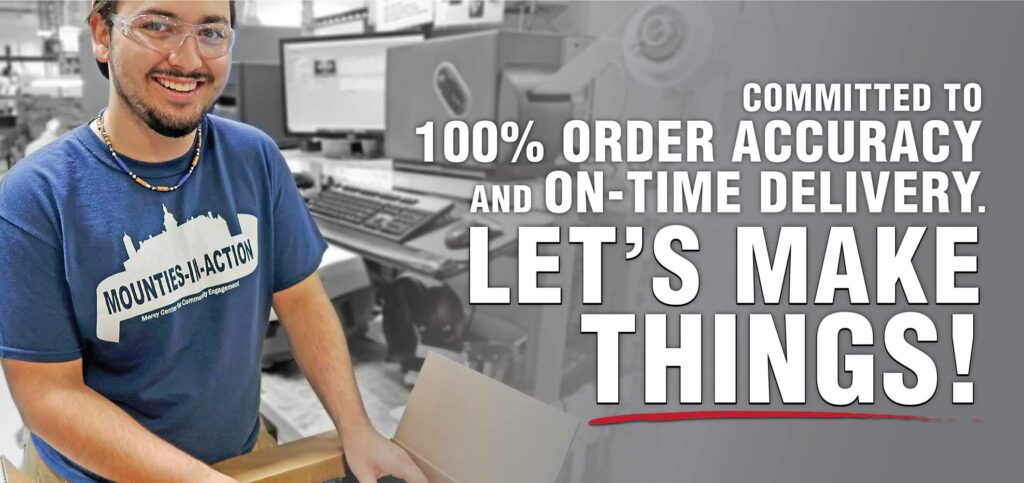
The long-held belief that it is cheaper to import goods from overseas no longer holds true as the current surging costs to import containers is still over triple that of pre-pandemic costs. Adding insult to injury, the freight industry has been upended by uncertain lead times and delays at overwhelmed ports.
Now more than ever, reshoring plastic injection molding and tooling domestically is the right choice in combatting these added costs.
Security Over Cost
The COVID-19 Global Pandemic brought the vulnerability of our global supply chain to the main stage.
In 2022, The New York Times reported moves by major automotive, tech & retail manufacturers to invest in reshoring their manufacturing & production operations back to the United States to reduce the effects of supply-chain issues on the sale of their products.
At York Imperial Plastics, our manufacturing facility is conveniently located within a short flight or drive from New York City, Philadelphia, Pittsburgh, Baltimore, and Washington, DC. Our convenient location to these major cities results in seamless access to raw materials, labor, and our customers without the headache of the overseas shipping delays and rising freight costs. By being close to our customers, we can ensure that our finished products arrive on time.
Be sure to check out York Imperial’s social media channels to peek inside life at #YIP
Made in America
In today’s post-pandemic world, consumers have shown that they prefer and will pay more for American-made products that create American jobs. Nearly three-quarters of respondents to a 2022 study conducted by The Harris Poll stated they seek out and intentionally purchase American-made products specifically labeled “Made in America.”
York Imperial Plastics’ injection molds are provided with Life of Program Tool Warranties. All molds constructed by York Imperial Plastics and built to our standards for longevity are warranted for the life of your program, as long as your products are manufactured in our facility.
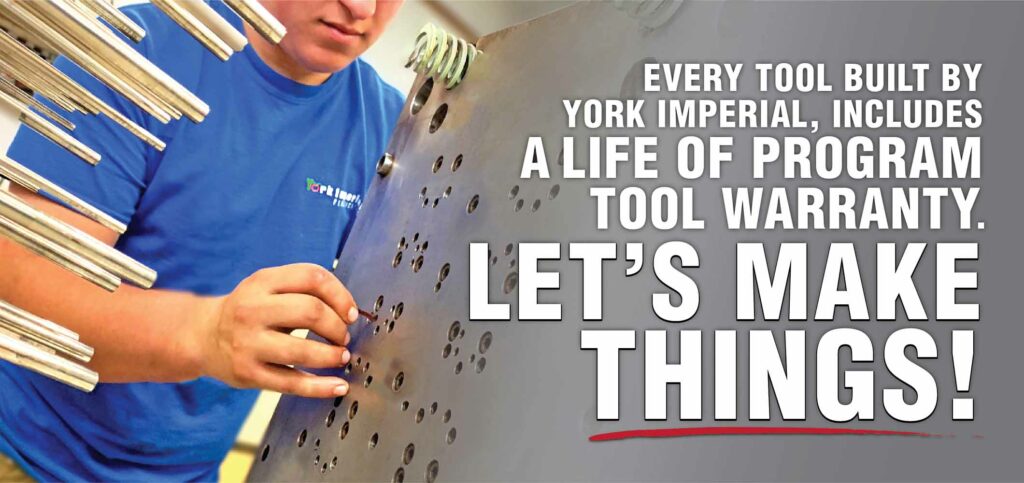
After your products have been manufactured at York Imperial Plastics, our team can assemble, test, and package your product for sale. Many of the products we manufacture ship “retail ready,” and never touch our customers hands. In addition, our shipping & receiving department prepares direct shipments to major retailers across North America placing your finished product directly in the hands of consumers.
Let’s manufacture something together!
We at York Imperial Plastics invite you to learn more about our injection molding capabilities by taking a tour of our family owned and operated state-of-the-art injection molding facility in York, PA to experience our day-to-day operations first hand and learn how we’ve been making ideas a reality since 1985.